Strain Testing Glass
With some simple equipment, you can check your future mirror for strain
before
you spend countless hours carefully crafting its surface to within
nanometers
of a parabola. Strain can cause glass to change shape over time,
destroying
the figure that was given to the surface. Severe and even mild
strain
should be completely removed by annealing, but this is not always the
case.
Also, mechanical operations performed on the glass (generating,
slicing,
significant grinding, cutting, etc.) can cause strain or release it,
the
latter causing at best a subtle change in the shape of the mirror, and
at
worst, breakage of the glass.
A simple test for strain generally requires three things:
1) a pair of polarizers (polaroid material), one piece
large
enough to cover most of the glass to be tested, and
2) a source of diffused white light
3) an uncoated mirror
I recently bought several pairs of polaroids, about 8" x 10" in size,
from
Surplus Shed (www.surplusshed.com). I also built two light boxes,
one
approximately 8"x10" square and the other approximately 19" x 23".
Both
boxes are 7.5" high, to permit incandescent 60W light bulbs to fit
vertically. One light bulb illuminates the small box, and four
light the large one.
Here are two pictures of the larger box, without and with the
white
plexiglass cover that serves as a diffuser.
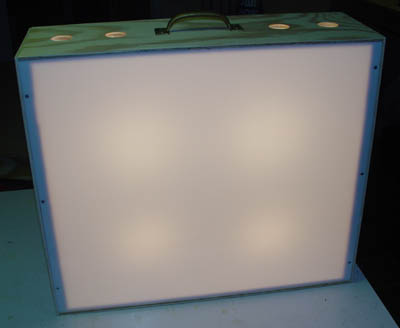
The smaller light box is completely covered by one of the polarizing
films. Then the pieces under test are set on top of the
polarizer, so that the polarized light passes through them. The
tester views the light through another polarizer, and he/she rotates it
to the point where it makes the background the darkest. At this
point, variations in brightness of the light coming through the mirror
are either due to marks on the mirror front or back, or due to strain.
This test is best done with the front and back of the blank
smooth and coated with a little oil to make the blank more transparent
if necessary.
The larger light box, shown above, is covered with a larger polarizer.
I got it from a company in Taiwan called 3DLens, here is a link to their linear polarizer film. It cost
~$70, arrived
after a few weeks, and is of excellent quality. When lit, the
plexiglass
in the larger box appears nearly uniformly lit.
Below is a photo of two small blanks under test. The blank on the
right is 3" in diameter, and shows only generation marks on the back.
The
blank is the same shade of gray all over, indicating that there is very
little
strain in it. The blank on the left is a 4.5" that had been
dropped - the large chip on the right side shows some color and
brightness variations
near it, indicating quite a bit of strain. A faint bright strip
radiates downward and to the left from the fracture, indicating some
strain in the
rest of the blank. Overall, this blank is not badly strained, and
will serve its function just fine in a low power telescope. The
fractured area is to be covered.
The photo below shows an 8" mirror with a little bit of strain.
The
strain is indicated by the pattern, resembling a plus sign (+), made by
the
darker area. This indicates minor to mild strain, as the
difference
in brightness is not that much. This level of strain can even be
caused
by having the blank at a different temperature than the air, and the
strain
will disappear as the blank equilibrates.
This blank is not bad, and I prefer to work on mirrors with this level
of strain or less (preferably less). The rectangular feature in
the center of the mirror is leftover adhesive from a label that had
been stuck to the back of it by the coater, and the other features near
the edge at the 1 o'clock
position and extending from 5 to 9 o'clock are on the back surface of
the
mirror. All of those are to be ignored, and only the behavior of
the
mirror as it darkens (due to the polarizer being rotated) is important.
Over the last few years, I have obtained many molded blanks and
machined/generated blanks from United Lens, and to date, NONE of them
have had any strain that is detectable using this test. Some
opticians claim there is no good source of well-annealed blanks, but I
disagree!!!
Below is an image of a 25" x 4.5"-thick blank. We think it is
Pyrex.
It is a stunning example of what this simple test can show. The
blank
is larger than the large light box, so parts of the mirror are not
illuminted
with polarized light. Some strain and numerous striae are visible
in
this blank, the worst striae I have ever seen. However, the blank
as
a whole is fairly stable, judging by the figure on the surface which
has
been there for quite a while. So, as long as it is not
mechanically
altered (regenerated, sliced, ground, etc.), I don't believe the
blank's
shape will change much. However, I can't say that for certain,
and
it's just the impression I get for this particular blank. Every
piece
of glass is different, so test them all and be careful.
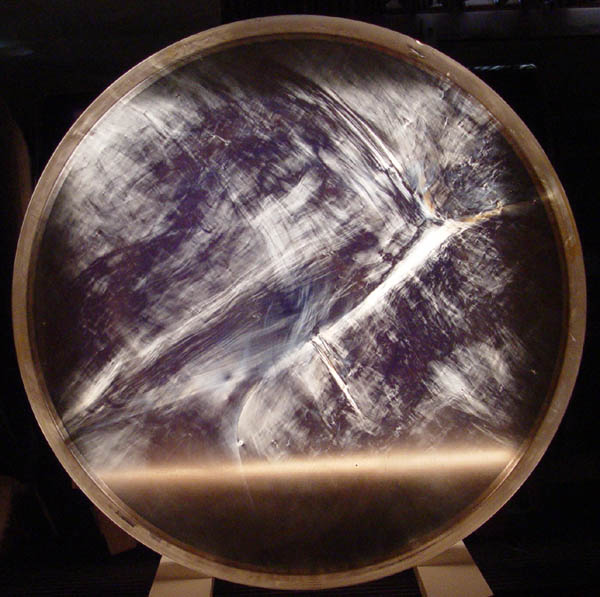
There are other ways to produce polarized light (such as by using
reflected
sunlight) and this technique, largely borrowed from others, is not the
only
way to test for strain. However, because I test quite a few
mirrors,
the investment in the setup has paid for itself many times over and has
provided
photos like the stunning example above.